Se quase tudo em nossa vida tem a ver com a mineração, imagine a quantidade de minerais e minérios necessária para produzir de lápis a fogão, de um punhado de clips a carro elétrico, de pasta de dente a celular... e por aí vão, os bens de consumo essenciais ao nosso dia a dia. E a demanda só tende a aumentar, já que a indústria é peça-chave na transição energética.
A extração de compostos como ferro, cobre, níquel, alumínio e lítio, entre outros, se dá por meio de processos extremamente complexos. Máquinas imensas perfurando o solo em busca de recursos. Algumas minas, por vezes, são maiores do que as áreas urbanas das cidades onde estão situadas e suas profundidades podem chegar a algumas centenas de metros.
Agora, tente imaginar o volume de resíduos gerado pelos projetos minerários. Para quem não conhece o setor, é ainda mais inimaginável. Montanhas e montanhas de terra, lama e rocha, acumuladas a céu aberto ou depositadas nas barragens.
Não à toa, entre os desafios impostos à mineração sustentável, está a redução da produção desses materiais. Nesse sentido, os últimos anos têm sido de avanços importantes. Das universidades e centros de pesquisa da própria indústria, saem estratégias de aproveitamento dos resíduos.
Eles costumam ser de dois tipo. Os chamados de estéril resultam da etapa inicial da mineração: quando o mineral é removido da lavra.
O segundo, conhecido como rejeito, é o que sobra do processamento do minério, depois de triturado e submetido a vários processos para separar o que será usado do que é apenas resto. Graças às inovações mais recentes, um material antes considerado de descarte, agora, passa a ter valor.
A Vale, por exemplo, passou a recuperar minério de ferro a partir de estéril e rejeitos de suas próprias atividades. Entre janeiro e junho deste ano, cerca de 2 milhões de toneladas do material já foram extraídos dessa maneira.
O processo resultou ainda em uma economia de aproximadamente R$ 100 milhões, ao eliminar algumas etapas da cadeia de descarte. A expectativa é de que, até o fim de 2024, um total de 6,7 milhões de toneladas sejam recuperadas assim.
A iniciativa faz parte de um ambicioso programa de mineração circular elaborado pela companhia. Foram mapeadas 100 iniciativas de reutilização de resíduos.
Entre elas está, por exemplo, o aproveitamento de 138 milhões de toneladas rejeitos da barragem Gelado, na Serra Norte de Carajás, no Pará, para a produção de pellet feed.
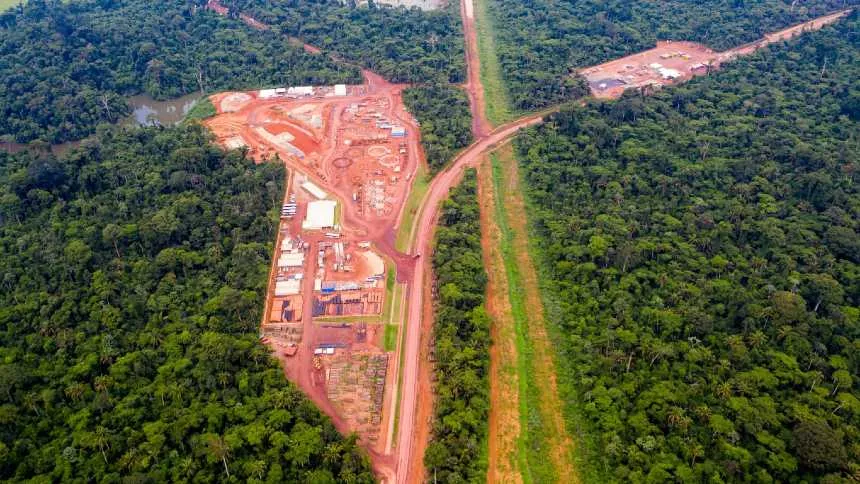
Espécie de pó de minério de ferro, o composto pode ser utilizado na composição de pelotas — as “bolinhas” de ferro aglomerado destinadas à siderurgia, para a fabricação de aço. Lá na planta paraense, o projeto é reduzir 62% do rejeito total, acumulados na barragem ao longo de 37 anos de operação.
“Até 2030, a meta é que cerca de 10% da produção anual de minério de ferro venha de mineração circular”, diz Bruno Pelli, diretor global de serviços técnicos de mineração da Vale, em entrevista ao NeoFeed. “E, em um cenário ainda mais otimista, queremos chegar a 20%.”
Da lama à construção civil
As pesquisas para reaproveitamento dos resíduos da mineração vêm ganhando força recentemente, mas já estão em curso há algum tempo. O coordenador do Laboratório de Materiais de Construção Civil, da Universidade Federal de Ouro Preto, em Minas Gerais, Ricardo Fiorotti, por exemplo, já atua na área há quase duas décadas.
Sob sua batuta estão linhas de desenvolvimento de produtos para a construção civil, obtidos a partir dos resíduos minerários. São eles concreto, argamassa, blocos, cerâmica e azulejos hidráulicos.
Outra aplicação é na substituição da brita, os fragmentos de rochas duras, originários dos processos de beneficiamento de blocos maiores, usados como base para pavimentos, por exemplo. É possível ainda usar os rejeitos na infraestrutura de rodovias, para a fundação de estradas, reforçando as camadas logo abaixo do asfalto.
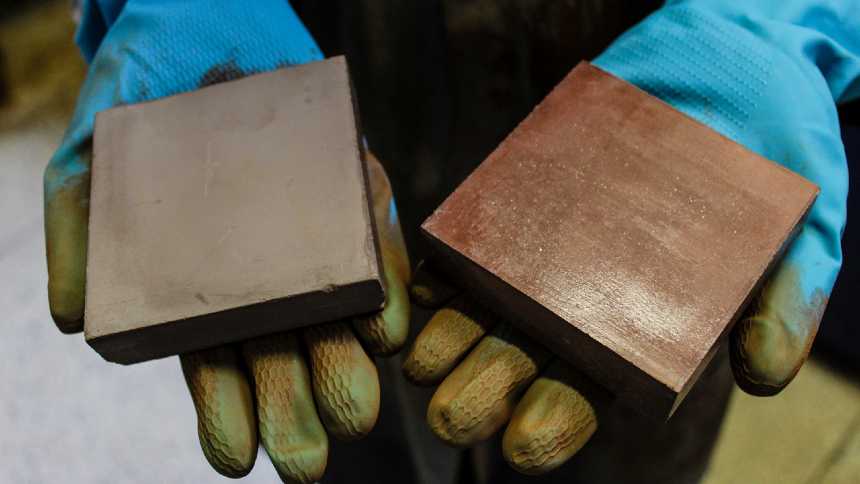
"O grande objetivo de nossas pesquisas é desenvolver soluções para que os rejeitos façam parte da cadeia de valor da mineração", conta Fiorotti. Os trabalhos do grupo que ele lidera, aliás, são realizados dentro de casas construídas com blocos e outros materiais feitos a partir de rejeitos.
A "areia sustentável"
Também em Minas Gerais, no município de Itabirito, a Vale mantém, desde 2020,a Fábrica de Blocos do Pico. Ali, são produzidos, anualmente, 3,8 milhões de itens para a construção civil, como pisos intertravados, blocos de concreto e placas de vedação, a partir de 30 mil toneladas de resíduos.
Além dessa unidade, em 2023, a Vale inaugurou a Agera, que produz areia, a partir do processo de produção do minério de ferro. Batizado "areia sustentável", o produto resulta de sete anos de pesquisas e, desde 2021, é usado como substituto da areia extraída do meio ambiente.
Segundo a companhia, desde então, já foram destinados ao setor de construção civil e a projetos de pavimentação rodoviária cerca de 2,1 milhões de toneladas do produto. A expectativa é comercializar aproximadamente 1,8 milhão de toneladas ainda este ano.
Além destas, a mineradora tem outras iniciativas em fase de testes. Entre elas, está um subproduto extraído do estéril triturado que pode ser usado para recuperar solos degradados pela agropecuária intensiva, o que pode fazer da mineração uma aliada da agricultura regenerativa.
Ao dar um fim mais “nobre” ao que antes tinha o descarte como destino, o programa de mineração circular da Vale promete evitar a emissão de 1,9 milhão de toneladas de CO2 até 2035 — o equivalente a retirar de circulação, por um ano, 1,2 milhão de automóveis populares.